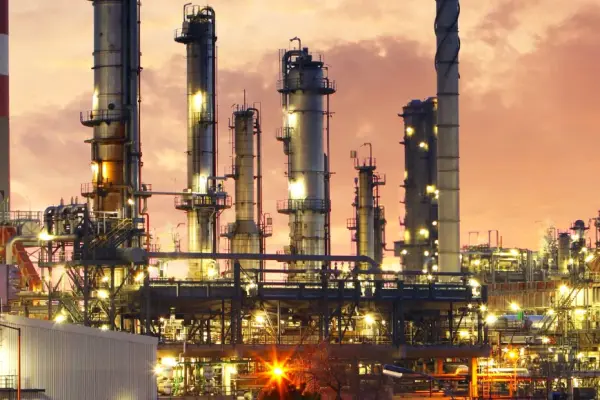
DEKRA Advisory & Training
What exactly is HAZOP? And how does a good HAZOP study perform?
What is a HAZOP?
The HAZOP method is a risk evaluation of the processes. It is intended for organizations in the chemical, pharmaceutical, food, oil and gas, nuclear, and other process industries. What exactly is HAZOP? And how does a good HAZOP study perform? Below you can read the answers to a number of frequently asked questions about our HAZOP method.
What is a HAZOP study?
The Hazard and Operability (
HAZOP
) methodology is a systematic team-based Process Hazards Analysis (PHA) technique that can be used to effectively identify and analyze the risks of potentially hazardous process operations. It is used during the design stages of a new process or project, for major process modifications and for periodic review of existing operations.
What is the purpose and approach of HAZOP?
The purpose of HAZOP is to prevent the release of hazardous materials and energy, followed by mitigation of the consequences should a release occur. It is essential for the team to identify all the hazards of the process being studied, not just the most obvious ones. Our approach is to use a semi-quantitative HAZOP that incorporates Layers of Protection Analysis (LOPA) to assess the reliability and number of safeguards.
What are the advantages of undertaking a HAZOP study?
HAZOP is a rigorous, structured, systematic and comprehensive method, and is adaptable to the majority of process industry operations. It fosters the exchange of knowledge and experience among the participants and enables companies to anticipate potential accidents.
What information must be gathered in preparation for a HAZOP study?
HAZOP requires a review of all the available Process Safety Information (PSI) as well as identification of any missing PSI necessary for an effective HAZOP analysis. This includes, but may not be limited to:
- Hazardous materials properties including combustibility, flammability, explosivity, reactivity, self-heating, toxicity, electrostatic properties
- Process description
- Process flow sheets
- Operating procedures
- Piping and instrumentation drawings (P&IDs)
- Equipment design specifications
- Pressure relief systems specifications
- Site and industry data concerning process-component failure frequencies and probabilities of failure on demand (PFD).
How long does a HAZOP analysis take?
Estimating the duration of a HAZOP is not, of course, an exact science; it requires a good knowledge of the methodology, complexity of the process, nature of the risks that can be identified up front and, of course, the idiosyncrasy of the group. In no case should a HAZOP be carried out without an estimated agenda, but it is not acceptable for the estimation to be rigid and not subject to modification (up or down) as necessary.
What is the end product of the HAZOP study?
At the conclusion of the HAZOP analysis, our process safety specialist will present the observations, findings, and conclusions of the analysis, and preliminary recommendations and suggestions of the HAZOP team to members of the site management. Shortly thereafter, our process safety specialist will submit a written draft report to the client outlining the HAZOP team’s recommendations and suggestions for improvements to the process based on the site’s experience and on recognized and generally-accepted good engineering practices. Following the receipt of comments from the client, a final report will be issued.
What mistakes are commonly encountered when conducting a HAZOP analysis?
Firstly, planning errors can negatively impact the HAZOP study. While an estimated time frame should be in place, lack of flexibility can lead to incomplete analyses. Another pitfall is insufficient, outdated, or missing information. In order to properly identify and address potential hazards, the HAZOP team must have access to timely and complete information. A lack of focus and discipline among team members is also a common problem. Allowing outside calls and interruptions during HAZOP meetings, as well as tardiness or absences hinders the team’s progress. The so-called “minimalist HAZOP” is yet another typical mistake. This refers to superficial studies where key words or parameters are omitted, repetitions are frequent or templates are used, all of which can short-circuit the brainstorming work that allows the team to uncover less obvious risks and hazards. Finally, the “bureaucratic HAZOP” is a subset of the minimalist version. Here the process is reduced to a formulaic box-checking exercise, resulting in repetition and hampering a deeper analysis.