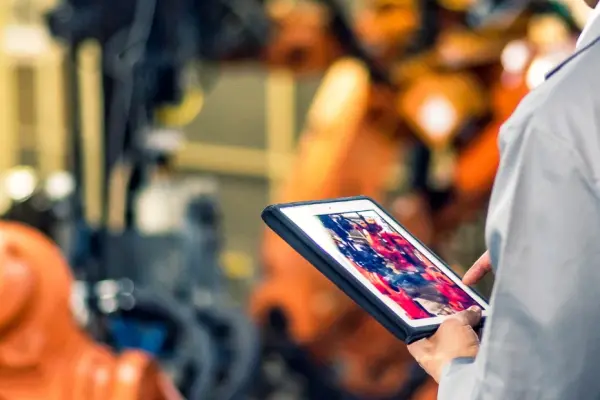
DEKRA Industrial Inspection
A fully comprehensive range of expert NDT services, worldwide.
Measuring corrosion and creep online
Strain monitoring with SPICA
Typically, operators or maintenance managers of power plants and refineries are responsible for pressure equipment. What are the possibilities and how can they benefit from the SPICA method?
Pressurized material is subjected to creep when operating at temperatures above approximately 400-450°C. The consumption of creep life can be evaluated by in-service evaluation standards. Due to the conservative nature of such an evaluation, the resulting life time consumption is in many cases much higher than the actual consumption. On the other hand, local creep exhaustion due to stress concentration is usually not addressed by this approach which causes a risk of overlooking regions with severe creep damage.
A more accurate approach of determining life time consumption and remaining life is determining the actual creep damage by measurement of the creep strain. SPICA is a method to perform such strain measurements accurately and during operation. Furthermore SPICA has the ability to monitor local creep life exhaustion, for example in the heat affected zone of a weld.
The benefits of SPICA
A more accurate determination of remaining life can save money. If, for example, it can be shown by strain measurement that creep life consumption is still low inspection intervals can be longer compared to the situation of higher consumed creep life. Also, the actual condition can be assessed during service, enabling planning of repair or replacement before upcoming inspections. Components that are ‚suspected‘ (e.g. having repair welds, or have long service life) can be monitored. For example, a plant being near the end of design life had SPICA installed sensors to monitor creep strain. This allowed the plant management to safely increase the steam temperature with a few degrees, yielding substantial extra income.
Why is SPICA unique?
SPICA measurements are carried out during operation, so, unlike replication, they are done independent of an outage. Also the results are, again unlike replication, independent of the assessor. Interpretation of creep damage of martensitic steels is uncertain using replication and will give warning only in a late stage. Conversely, SPICA strain measurement is material-independent and, in addition, allows for local strain measurements in the heat affected zone which act as early warming as problems normally arise there first. Strain gauges are not able to detect this local strain in the HAZ because the gauge strain is measured- and averaged over a larger length across the parent material, HAZ and weld material. SPICA does not involve cables and is very robust: sensors cannot be easily destroyed like strain gauges.
Steps in a SPICA-project
SPICA sensors are installed at selected critical locations (DEKRA can provide an advice on which locations are critical). A ‚Hot Measurement‘ consists of photographing the sensor surface using a SPICA camera. The measurement is referred to as ‚Hot‘ since it is performed during operation. After subsequent ‚Hot Measurements‘, image correlations can be made from which strain and strain rate are determined. Based on a strain criterion, creep life consumption can be determined. If first measurements are not taken from the start of service, creep life consumption until the first measurement can be estimated by in-service evaluation standards. In summary, the following steps are taken:
- Selection of critical locations
- Mounting of sensors
- Hot measurements
- Digital correlation analysis
- Evaluation of strain and strain rate
- Determine creep life consumption
Typical application
SPICA is an in-house development as a method for in-service strain measurements in industrial plants. SPICA sensors have applied in plants throughout Europe, the Middle East, South-Africa, Japan and China. Plants where SPICA is applied are power plants, refineries and chemical plants. Typically, 5 – 20 sensors are applied per plant at components like Y-pieces, T-pieces, girth welds, headers, bends, HP steam valves, and hydro cracking reactors.