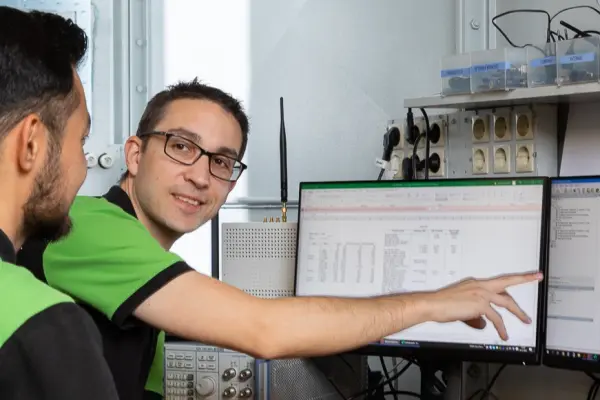
DEKRA Industrial Inspection
Looking for reliable retaining rings inspection? Find out here.
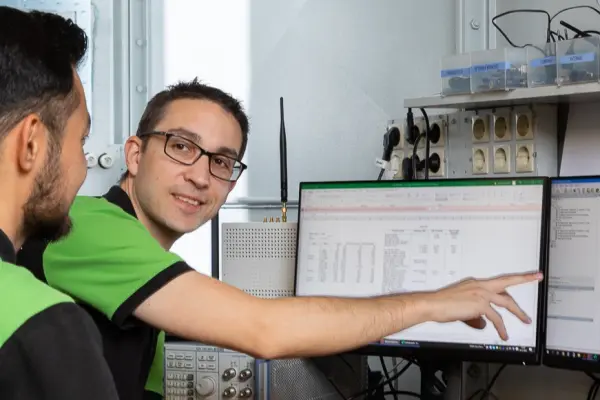
DEKRA Industrial Inspection
Looking for reliable retaining rings inspection? Find out here.
Retaining Ring Inspection (KIRR)
Saving time, effort and money with Non-Destructive Testing
The generator is one of the most crucial parts of a power plant, since it is where the mechanical energy is converted into electric energy. It is therefore essential that the generator is always in optimum condition
Among the critical components are the retaining rings at each end of the rotor. These are susceptible to damage as a result of specific chemical influences and mechanical or electrical forces. However, replacing the rings involves substantial costs. The DEKRA inspection system for retaining rings (KIRR) represents a cheaper yet equally effective alternative. The system has already been used to inspect over 1,600 generator retaining rings in 25 countries worldwide.
The KIRR retaining ring inspection can be performed in approximately 2.5 shifts, depending on the size and accessibility of the generator. If required, multiple teams can be sent to reduce inspection time to 24 hours. Removal of the shields, blades, coolers and electrical safety, approved scaffolding, illumination and cleaning is the responsibility of the Client. Removal of a coating on the ring is not required.
Tests that are performed
The KIRR manipulator is equipped with several probes whereby different tests are performed simultaneously:
- Ultrasonic testing includes UT-TOFD for the ring’s inner surface and ring’s volume, scanning for both axial and circumferential flaws. UT-PE (Pulse Echo) is applied for high accuracy in shrink fir zones.
- Eddy current Testing (ET) for the outer surface with high accuracy.
Dye penetrant on removed rings is discouraged: cracks in the shrink zone may close due to removal. Note: DEKRA is an independent company, not affiliated to any OEM or repair shop.
What type of generators and machines can be tested?
The height of the probes is 8 mm which allows for testing of almost all generators. The chain link system to mount the KIRR manipulator is suited for rings of a diameter of > 600 mm. In case of rings with ‘nose area’ (the sloping part of the ring where the outer diameter becomes smaller): this can be tested separately, maximum slope angle is 45°. We have performed retaining ring testing for more than 25 years, in which we have tested over 100 different generator (sub) types, including larger H2-cooled generators that are difficult to access (like THDD-type generators) and (in case of removed rotor) generators with rings with cooling holes, as well as exciter motor rings. Also see our reference list download at the bottom of this page.
Service
The KIRR system is adjustable to fit virtually all generators and large motors. This flexible system combined with our extensive experience in this field allows us to draw up the inspection plan on site, without detailed information being required beforehand. If required, the inspection can be performed within 24 hours. Ultrasonic crack detection is focused on the shrink-fit areas and wall thickness steps. Damage, such as stress corrosion cracking and top tooth cracking, is detected. In addition, eddy current scanning is added to accurately map the outer surface. The ring’s coating is left in place. If cracks are discovered, ring geometry and flaw data are used in an FEM computer model to calculate the residual lifespan. Furthermore, we establish the inspection interval for monitoring purposes.
Specifications
The KIRR system can be applied on generators with a ring diameter of 600mm and upwards. In-situ test characteristics:
- Minimum gap between retaining ring and stator: 8mm
- Technique: UT-TOFD, UT-TRL and ET scanning
- Surface: 360° circle and 1-10mm pitch
- Defect heights of 0,5 mm and upwards are detected
- Typical test duration for two rings in-situ: 24 hours
Background
A retaining ring has a long lifespan and often lasts for the entire life of the generator. However, the smallest of cracks in the retaining ring poses a risk to safety and could result in extremely costly damage. To avoid such disastrous consequences, many manufacturers recommend that the retaining rings are replaced periodically – an expensive exercise which can cost up to a million euros. DEKRA’s KIRR offers a cost-effective alternative. The system detects and analyzes flaw indications in the retaining ring, enabling you to determine whether the retaining ring needs to be replaced. Furthermore you can keep a close eye on newly detected flaw indications in retaining rings which do not yet need replacing and monitor their condition during future operation. One crucial advantage is that it is no longer necessary to disassemble the rotor and the retaining rings for inspection purposes, which in turn yields cost savings of up to EUR 200.000.